摘 要:本文针对捷克YORK公司离心式制冷机组主传动轴断裂的原因进行了理论分析,提出了解决方案和改进措施。
关键词:离心式制冷机组;主传动轴;断裂;分析;措施
一、制冷机压缩机的工作原理
压缩机通过摩擦联轴器与转速为2975r/min的6kV主电机相联,由主传动轴带动大齿轮,通过小齿轮轴使转速增至10902r/min,带动铝合金叶轮高速运转,使氟里昂压力升高,达到冷凝条件。
主传动轴与轴套通过轴端的12条M8×1.25mm的高强度螺栓连接,并通过其传递扭矩;轴套与大齿轮采用过盈配合(制造厂家以组合件形式提供),轴套与轴之间的空腔安装双端面机械密封;叶轮通过3条M12×1.25mm高强度螺栓与小齿轮轴连接并定位,见图1。
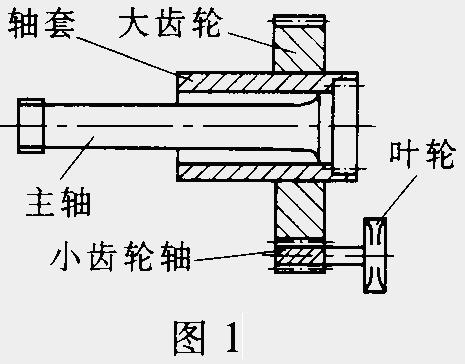
二、故障情况
1997年10月2日,92C103机组的主电机电流陡降,冷凝压力迅速降低,压缩机停止运行;且有大量润滑油从主传动轴密封处喷出。解体检修发现主传动轴(结构见图2)从A-A端面处断裂,断口呈凹凸状(见图3)。
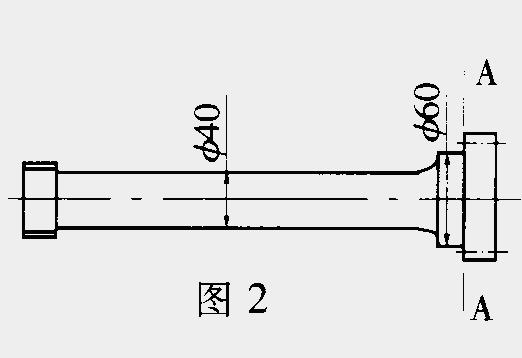
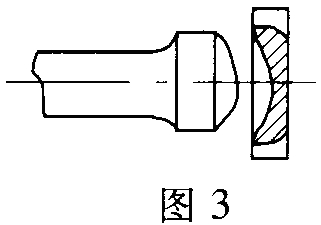
三、原因分析主传动轴断裂的可能原因是,强度不够、结构不合理、装配精度和零部件加工精度不够。
1.强度
从断裂位置来看,主传动轴断裂处直径为φ60mm,而Z小直径为φ40mm处的轴颈未断裂,由此可以判断主传动轴断裂不是因强度不够造成的。
2.结构
从图2可以看出断裂处为直角过渡,是应力集中的地方。而且主传动轴与轴套的配合端面对轴线无垂直度要求,且配合精度低,因而加大了主传动轴的运行载荷;同时机组的四个滑动轴承与轴套的实际间隙值为0.19mm,在检修规程允许范围0.15~0.20mm的上限,也加大了主传动轴的运行载荷。
3.裂纹形成及扩展过程主传动轴断裂面呈凹凸状,且有放射状组织存在(见图4)。这种断口形式是由疲劳裂纹产生的,因为疲劳裂纹总是首先发生在应力集中的地方。
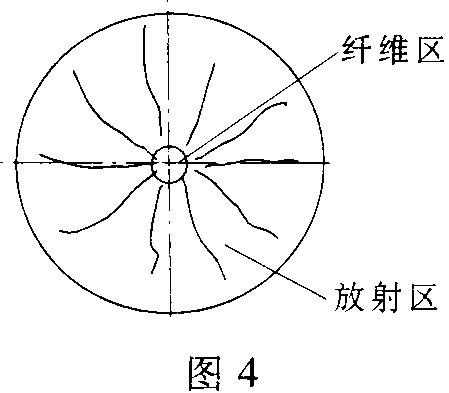
材质内存在第二相或夹杂物,以及A-A端面和直径为φ60mm轴颈的表面粗糙度较低是导致裂纹源的可能原因。加之组成金属的某些晶粒在Z大剪应力作用平面内产生滑移,在交变载荷作用下,随着疲劳过程的进行,原有滑移线的滑移量增大,逐渐形成滑移带。随着滑移带的加宽加深,在表面出现“侵入沟”和“挤出带”,从而形成裂纹源。
当传动轴出现的初始裂纹小于临界裂纹尺寸时,在交变载荷作用,尤其是机组频繁启动(从安装使用到断裂前反复启动了约40次)的情况下逐渐扩展,直至达到临界裂纹尺寸而断裂。
四、结论
通过上述分析可知主传动轴断裂不是强度不够所致,而是由于结构设计不合理、加工和装配精度低、启动次数频繁等原因,在应力集中处产生裂纹源,然后在交变载荷和机组运行时其他部件给予的附加载荷作用下逐步扩展,达到临界裂纹尺寸造成的。
五、处理措施及效果
1.将轴上A-A端面的直角过渡改为圆角过渡(取r=2.5mm)。但注意与其装配的轴套的内圆应倒角,且以不影响主轴的装配为准。
2.为减少主传动轴运行时的额外载荷,在A-A端面增加了垂直度和粗糙度要求。同时适当减小了四个滑动轴承的装配间隙(实际为0.16mm),但以保证机组的安全运行为前提。
3.加强工艺优化,提高操作水平,加大巡检频率,减少机组开停次数。
采取了相应措施后,3年多以来未再发生类似事故。