作者:闵青松
(蛇口集装箱码头有限公司)
摘 要:小车减速箱是桥吊牵引机构的重要组成部份,保证减速箱在工作中的正常运行,对提高桥吊的工作效率和安全性能有着重要意义。对齿轮轴断口进行宏观分析,结合有限元和材料力学等方面,深入地分析减速箱齿轮轴断裂原因,同时提出合理化的处理方案和改进措施。
关键词:港口;牵引小车;减速箱;齿轮轴;疲劳断裂;断口
2008年7月至2011年4月期间,SCT二期桥吊共4台牵引小车减速箱在正常工作中发生第300齿轮轴键槽根部径向整体断裂事故,造成各级传动齿轮和轴承、箱体不同程度损伤。发生断轴事故的4台牵引小车减速箱平均运行时间为11120h。该桥吊于2003年投入生产,小车牵引机构减速箱为某进口品牌,作为世界顶级动力传动设备制造商,各方面技术成熟,制造工艺应该是不存在问题,如果按“减速箱保养规范”进行保养维修,理论上的使用寿命至少可以达到15年~20年以上。但是展现在面前的两台减速箱在同一时间段、同一根轴和同一位置发生断裂,不得不让人深思,去寻找问题的根源。本文通过对断轴部位进行分析,找出断裂的根本原因,对减速箱其中缺陷进行整改、修复,在确保桥吊安全的情况下提高生产力。
1 减速箱断轴原因分析
1.1电机输出扭矩现场监测
该型桥吊使用ABB生产的三相交流异步电机,其主要参数为:V=500,Hz=60,P=320kW,r/min=1750,A=474。工作现场观察电机驱动输出扭矩实际状况,发现在小车启动时输出扭矩Z大,尖蜂扭矩达到101.67%,(图1)小车均速运行时输出扭矩在20%~70%之间。
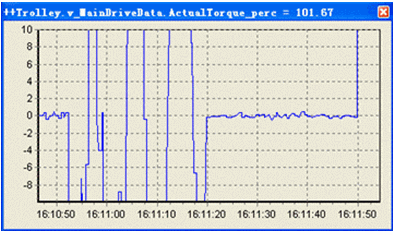
图1 小车电机输出扭矩示意图
1.2断口宏观分析
齿轮轴断口表面金属平滑,有非常明显的弧型花纹,Z终瞬断区域的,放射状花样清晰可见,瞬间断裂区的面积仅是轴的整个面积的五分之一左右,属于典型的高周疲劳断裂(见图2)。断口由疲劳裂源区、裂纹扩展区和瞬间断裂区等三个区域组成。
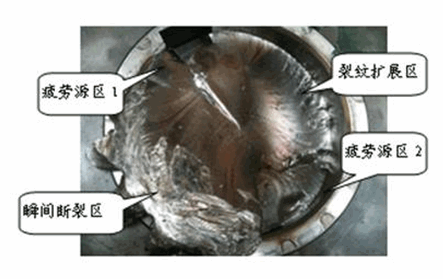
图2 齿轮轴断面裂纹源区图
齿轮轴在疲劳载荷作用下,其表面应力Z大,轴的中心部位应力Z小。疲劳源首先在表面形成,然后产生宏观裂纹,同时该裂纹沿着于Z大正应力相垂直方向扩展,宏观裂纹的两侧在交变载荷作用下,反复挤压、分开,形成断口的光滑区,到Z后瞬间断裂。
仔细观察断口裂纹源区(见图2),不难发现该轴Z早期初始疲劳源区在键槽的根部(图2源区1),应力Z大区域产生疲劳源。在交变应力的继续作用下,初始裂纹处的应力集中促使裂纹扩展,这时应力集中较大,轴的周边部位产生新的裂纹源(图2源区2)。两端裂纹源同时快速朝着同一方向集中靠拢,当两处裂纹源集中到一点时,齿轮轴承载面积不能承受牵引小车载荷冲击,产生瞬间脆性疲劳断裂。
2 用有限元分析软件ALGOR对断轴分析
2.1减速箱材质
减速箱 P=320kW,n1=1750/min,n2=66.89/min 第3级齿轮轴直径为130 mm,轴材质为:17CrNiMo6,主要化学成分和力学性能:
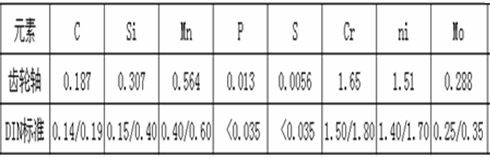
表1 齿轮轴材质化学成份
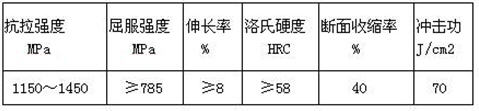
表2 齿轮轴材质力学性能参数
2.2减速箱300轴图纸(见图3)

图3 齿轮轴零件图
2.3CAD软件建模
根据减速箱300轴图纸实际尺寸建立轴的三维模型,完全真实反映该轴外型特征,见图4、5。
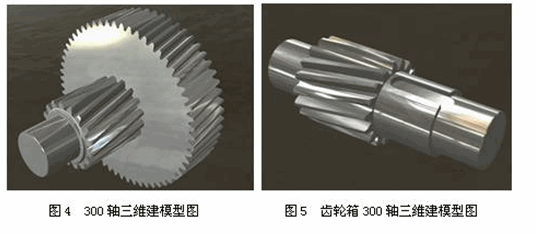
2.4单元类型选取和网格生成
该模型为典型的三维实体结构,需要采用实体单元模拟,ALGOR软件提供了全自动的六面体、四面体以及混合网格的高度智能化的划线功能,即使不进行任何控制,也可以生成非常复杂模型的高精度的网格,保证计算的高效性和高精度,见图6。
ALGOR的自动网格生成器可以非常智能地生成以六面体为主的网格,只要设置细化级别就可以控制网格密度。
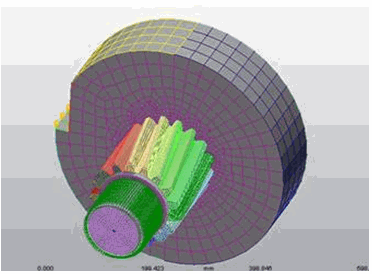
图6 ALGOR软件生成的300轴装配网络模型图
2.5载荷、边界条件的确定
为简化模型计算量,大齿轮外表特征简化,模型类型设定为线性静力分析,即小车启动的一瞬间的状态,齿轮轴处于静止状态,轴端轴承为调心滚子轴承,故轴承支座可以认为是铰支座,设边界条件为铰支座。
2.6线性静力分析结果。
图7为线弹性情况下得到的模型等效应力分布。从计算结果来看,Z大等效应力为549MPa,比较(见表2)所示的材料参数,模型的Z大等效应力小于该模型材料的屈服极限785MPa,说明屈服强度满足要求。
2.7疲劳寿命分析
ALGOR软件提供专用疲劳分析模块,可以预测复杂多重交变载荷作用下结构的疲劳寿命,同时可以提供直观的向导功能,来完成疲劳分析。
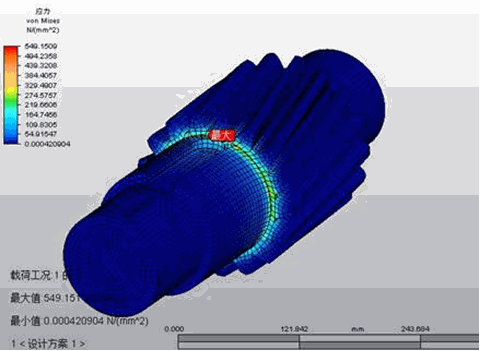
图7 300轴软件线性静力分析结果图
2.7.1疲劳分析方法的确定
常用的疲劳分析方法有两种,即应力寿命法和应变寿命法。应力寿命法基于S-N曲线(应力-循环曲线,应力幅值对应的疲劳循环次数),假定应力处于弹性范围内,适用于疲劳循环次数10000次以上,尤其是100000次以上的情况。应变寿命法基于E-N曲线(应变-循环曲线,类似于S-N曲线),可以考虑材料的塑性变形,对于可能引起局部屈服的循环载荷作用下的疲劳计算精度更高。
由于该模型线性计算结果的等效应力为549MPa,小于材料的屈服极限785MPa,应力处于弹性范围内,因此采用应力寿命法进行分析,设计循环次数为1000000次。
2.7.2S-N曲线的确定。
应力寿命法需要知道材料的S-N曲线,fatigue wizard能够根据输入的材料性能和材料类型确定一条S-N曲线,材料性能参数包括弹性模量、抗拉强度、磨光疲劳极限、极限循环次数,材料类型为钢材,见图8。

图8 300轴材料的S-N曲线图
3.7.3载荷曲线确定
在实际工作中小车运行真实情况启动、停止线性状况,所以分析过程中采用正弦载荷曲线,见图9。

图9 正弦载荷曲线图
2.7.4疲劳极限修正因子的确定
S-N曲线通常来自于对标准的磨光试件进行的疲劳试验。将这种试验数据应用于实际的工作环境时需要进行一定的修正。这种修正通过在试验疲劳极限上施加修正因子实现,由于齿轮轴为加工件,所以修正因子为0.56。
2.7.5疲劳寿命分析结果
疲劳寿命分析结果在fatigue wizard处理环境中查看到计算结果的多色显示图和交通灯图。交通灯图中的红色代表破坏,黄色代表临界区域,绿色代表安全区域。
fatigue wizard预测的该轴疲劳破坏周期为3670~2560000次,按照断轴减速箱平均使用寿命11120h。每小时吊箱30个,每吊一个箱小车启动和停止6次计算,减速箱疲劳破坏周期为2001600次,说明以上计算是精确的。
3 减速箱轴断裂改进方法及意见
由以上数据分析:减速箱轴由于日积月累疲劳导致断裂,应力集中是造成减速箱轴断裂的主要原因,主要还是轴的疲劳强度(构件抵抗破坏的能力)和稳定性(构件保持原有平衡形式的能力)的问题。当然也可能由于平常的作业人员吊箱的过程中需要反复使用启动、停止,小车负载后的冲击力,造成应力集中使齿轮轴疲劳断裂。
Z关键点还是在于轴的承受能力上。建议对减速箱现有的300齿轮轴,由实心轴改造为加强型实心轴。提高其强度和稳定性,这样可以达到想要的结果,增长其使用寿命。虽然会增加减速箱的维修成本,但是从长远利益上考虑能较大提高减速箱的安全性能和公司生产效益。
参考文献
[1] 钟群鹏,赵子华.断口学.北京:高等教育出版社.2006.6.
[2] 李育锡主编.机械设计基础.北京:高等教育出版社.2007.4.
[3] 许本安,李秀治主编.材料力学.上海交通大学出版社.1988.6.