作者:吴成伟
(万向钱潮股份有限公司)
翼型轴承座是汽车上的重要零件,如图1所示。其材料为20CrMnTi钢,工艺流程为:机加工—渗碳缓冷—重新加热淬火—回火—磨削。热处理技术要求为:磨加工后有效硬化层深0.80~1.20mm,表面硬度58~64HRC,心部硬度25~45HRC,表面残留奥氏体量不超过35%。
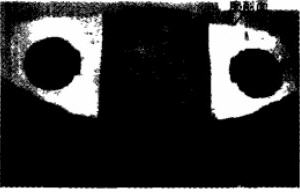
图1 翼型轴承座
1 硬度、金相分析及化学成分分析
翼型轴承座磨削后用磁力探伤检查出裂纹,裂纹方向与磨削方向垂直,裂纹极细,每个磨削平面多达3条裂纹。沿裂纹及磨削面垂直的方向用线切割机切样,并与未磨削加工面切样对比分析。制样发现,裂纹深0.4mm,裂纹穿晶开裂,裂纹起始端有撕裂现象,宽度5μm左右,长0.2mm,裂纹扩展部分极细,沿晶界扩展,长度0.2mm,对试样的磨削面和未磨削面表面洛氏硬度和显微硬度、心部硬度、有效硬化层、金相组织、化学成分进行了检测,结果如表1。由表1可见,化学成分及热处理各项指标均符合技术要求。磨削表面硬度为60.5~61.5HRC,比未磨削面的硬度63.5HRC低2~3HRC,磨削表面显微硬度Z低降低至569HV,而未磨削表面Z低为797HV。把裂纹试样用4%硝酸酒精侵蚀后在显微镜下观察,试样表面有一层极薄的白亮层(约2μm),试样表面用1.96N(0.2kgf)载荷检测的显微硬度比用9.8N(1kgf)载荷检测的显微硬度要高60HV。磨削试样侵蚀后颜色较深,有明显的磨削回火现象,金相组织为碳化物、回火马氏体和残留奥氏体,如图2b;而未磨削部位试样经腐蚀后颜色较浅,金相组织为弥散分布的球状碳化物和回火马氏体,残留奥氏体量少于18%,如图2c。
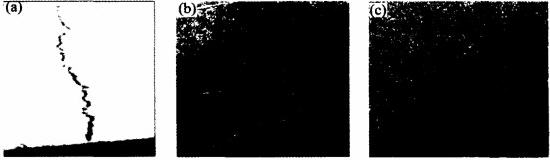
图2 轴承座显微裂纹形貌及组织 ×400
(a)磨削裂纹(未腐蚀);(b)磨削裂纹处金相组织;(c)未磨削处金相组织
表1 试样分析结果
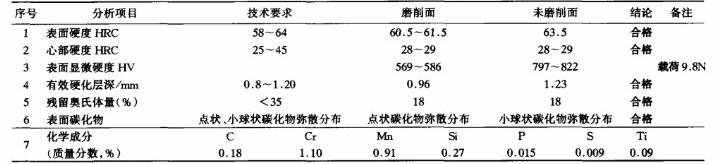
2 渗碳层硬度梯度
对磨削部位和未磨削部位的渗碳淬火硬化层硬度梯度进行了测量,结果见图3所示。从磨削部位的硬度梯度曲线看,硬度梯度曲线有明显的低头现象,Z高硬度出现在250μm处的次表层,表层50μm处的硬度为610HV,比次表层250μm处的硬度745HV低135HV,比未磨削部位表层硬度822HV低212HV(约9HRC)。磨削部位表面硬度用9.8N(1kgf)载荷检测为569~586HV(相当于54HRC),比未磨削处表层硬度822HV低236~253HV。未磨削表面的硬度梯度曲线没有低头现象,Z高硬度在表层,说明磨加工时产生大量的热,影响磨加工面深约0.3mm。
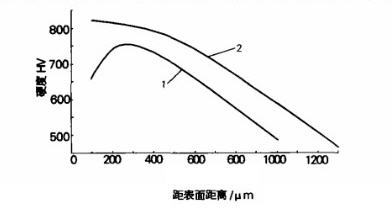
图3 渗碳层的硬度分布
1.磨削表面;2.未磨削表面
3 原因分析
(1)裂纹产生的主要原因是磨加工时磨削过烈(即磨削进给量大,砂轮自锐性差,冷却不足等),产生大量的热,使磨削面产生回火,严重时发生组织转变形成二次淬火马氏体,使工件在渗碳淬火时形成的表面压应力变为拉应力,从而产生磨削裂纹。
(2)轴承座表面硬度过高也是产生磨削裂纹的原因之一,未磨削表面的硬度高达6315HRC,显微硬度高达822HV,虽在公差范围内,但已接近公差上限,Z好将表面硬度回火控制在60HRC左右。
(3)控制工件表层的碳化物形态和数量,块状碳化物和网状碳化物容易引起磨削裂纹。
4 改进措施
改进磨削工艺,减少磨削余量;改进磨削方法,减少进给量,增加进给次数,定时修整砂轮,调整磨加工砂轮转速和往复运动速度;在确保表面硬度符合技术要求的前提下,适当提高热处理回火温度,控制表面碳化物。
来源:《金属热处理》